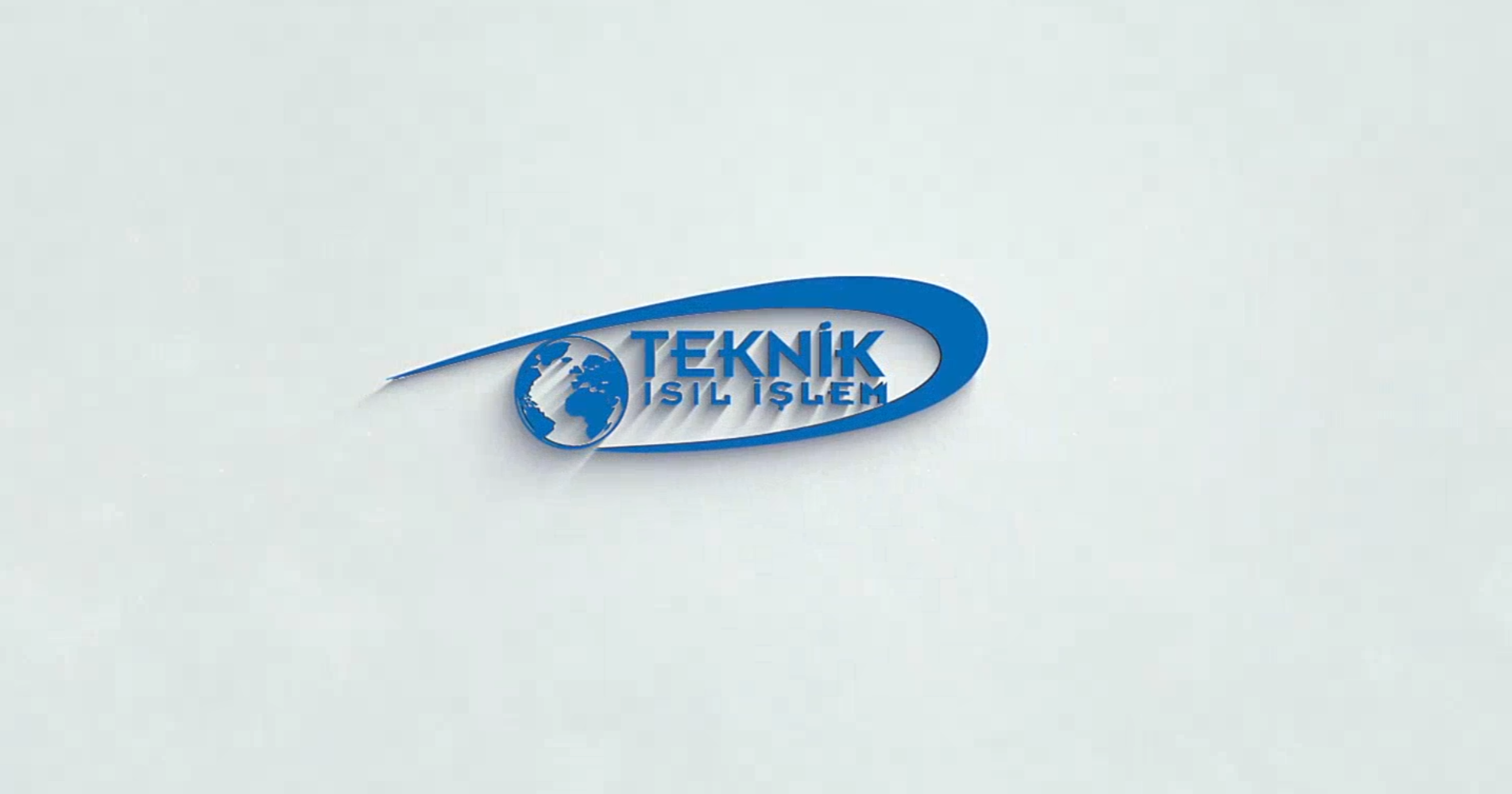
Teknik Isıl İşlem'e Hoşgeldiniz
36 yıllık tecrübesi ile Teknik Isıl İşlem olarak,
- Sementasyon Metodu ile Yüzey Sertleştirme
- Islah ısıl işlemi (Kontinü Fırınlarda)
- İndüksiyonla Yüzey Sertleştirme
- Karbonitrasyon Metodu ile Yüzey Sertleştirme
Proseslerini istenilen sürede ve kalitede gerçekleştirmek için bütün sanayicilerimizin hizmetindeyiz.
Teknik Isıl İşlem: Güvenilirlikte 36 Yılın Tecrübesi!
1987 yılında kurulan Teknik Isıl İşlem, sanayi sektöründe 36 yıldır üstün kalitesini koruyor. Sektördeki uzmanlığımızla, atmosfer kontrollü fırınlar, indüksiyonla sertleştirme tezgahları, kontinü fırın ve tuz banyoları gibi geniş bir yelpazede ısıl işlem proseslerini başarıyla gerçekleştiriyoruz.
Müşterilerimizin güvencesini en üst seviyeye taşıma amacıyla 2009'da ISO 9001:2008 kalite yönetim standardını benimsedik ve bu standartları sürekli olarak uyguladık. Ardından, 2022'de kalite çıtamızı daha da yükseltme hedefiyle ISO 9001:2015 belgesini aldık
Devamı